Case Study: Successful Implementation of Maintenance Scheduling Systems in Juiz de Fora
fp
Introduction to Maintenance Scheduling Systems
In today's fast-paced industrial environment, the need for efficient maintenance scheduling systems has become increasingly critical. This is particularly true in Juiz de Fora, a city known for its industrial activities, where businesses strive to maintain operational excellence. Implementing a maintenance scheduling system can significantly enhance productivity, reduce downtime, and extend the lifespan of equipment.
The implementation of such systems requires careful planning and execution. In this case study, we explore how one company in Juiz de Fora successfully integrated a maintenance scheduling system to streamline their operations and achieve remarkable results.
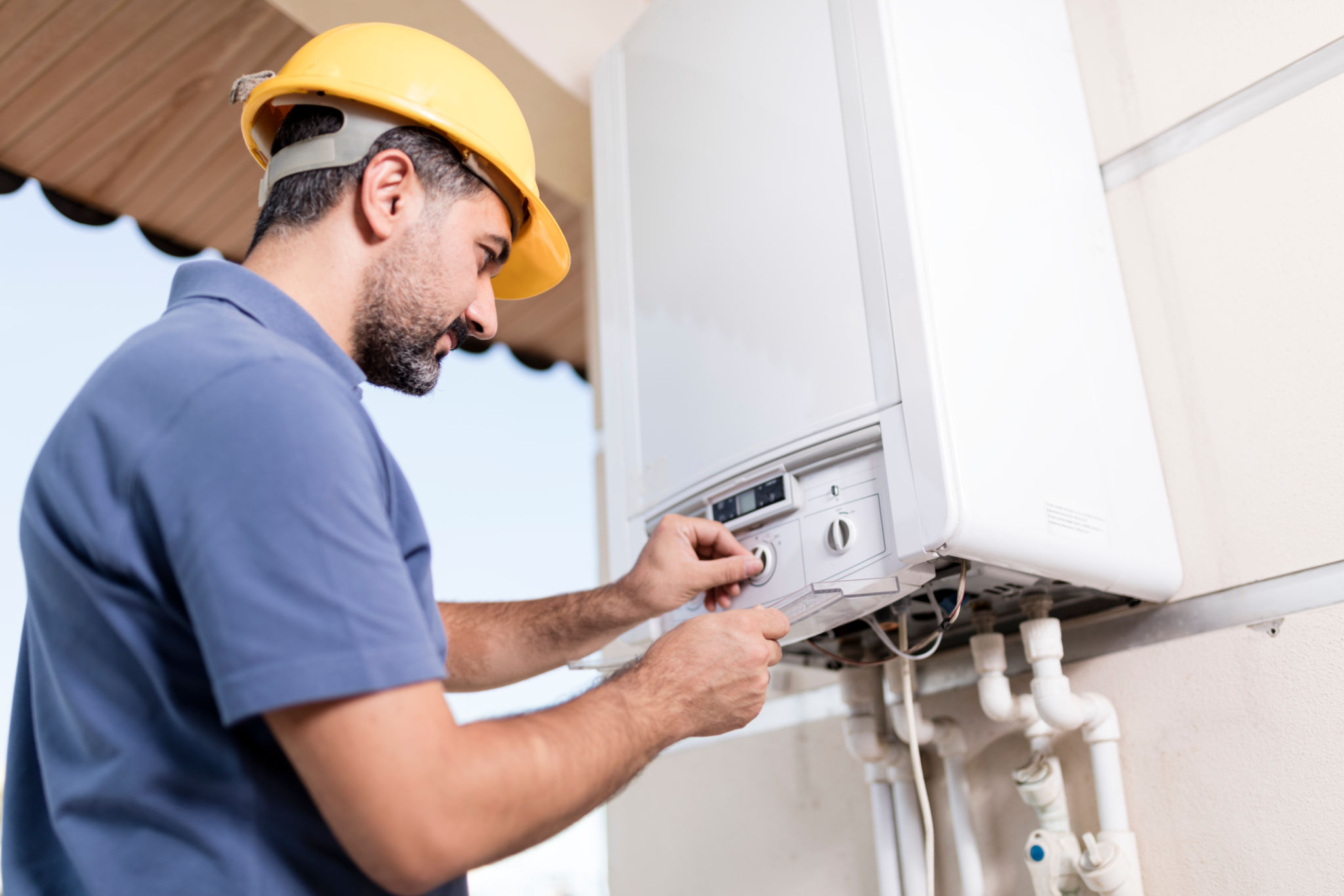
Challenges Faced Before Implementation
Before adopting a maintenance scheduling system, the company faced several challenges. Unplanned equipment failures were frequent, leading to costly downtime and disrupted operations. Maintenance tasks were often reactive rather than proactive, creating inefficiencies and increased operational costs.
Furthermore, there was a lack of coordination among teams, resulting in poor communication and delayed responses to maintenance needs. The absence of a structured system made it difficult to track maintenance activities and predict future needs accurately. These challenges underscored the necessity for a robust solution.
Choosing the Right System
The company embarked on a mission to find a system that could address their specific needs. They focused on solutions that offered user-friendly interfaces, scalability, and integration capabilities with existing systems. After thorough research and consultations, they selected a system renowned for its reliability and comprehensive features.
The chosen system promised to transform their maintenance operations by providing real-time data insights, automated scheduling, and enhanced team collaboration. The implementation phase was meticulously planned to ensure minimal disruption to ongoing activities.

Implementation Process
The implementation process was carried out in several stages. Firstly, key stakeholders were trained on the new system to ensure smooth adoption. This included training sessions and workshops aimed at familiarizing employees with the software’s functionalities.
Next, the system was integrated with the company's existing infrastructure. This integration was crucial for seamless data flow between different departments and systems. The transition was carefully monitored, with regular feedback sessions to address any concerns or technical issues.
Results and Benefits
Post-implementation, the company witnessed significant improvements in their maintenance operations. The scheduling system enabled predictive maintenance, reducing unexpected equipment failures by 30%. This proactive approach not only minimized downtime but also extended the lifespan of critical machinery.
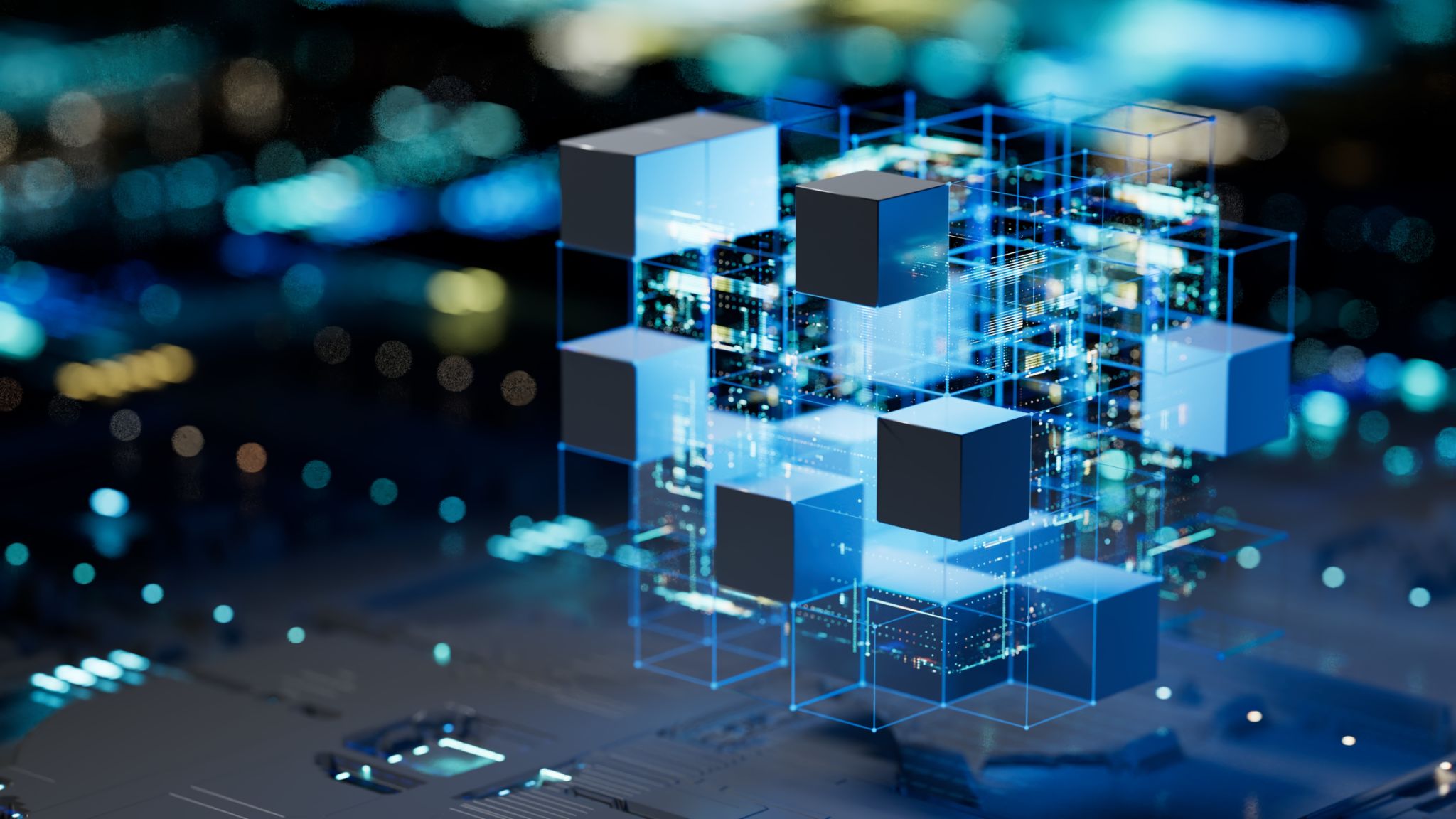
Moreover, the enhanced communication facilitated by the system resulted in faster response times and improved coordination among teams. Maintenance tasks were executed more efficiently, leading to an overall boost in productivity and cost savings.
Lessons Learned
This case study highlights several lessons for other businesses considering similar implementations. Key among them is the importance of selecting a system tailored to specific operational needs and ensuring thorough training and support for all users involved.
Additionally, ongoing monitoring and feedback are essential to continually refine and improve the system's performance. By fostering a culture that embraces change and innovation, companies can maximize the benefits of maintenance scheduling systems.
Conclusion
The successful implementation of a maintenance scheduling system in Juiz de Fora serves as an inspiration for other companies facing similar challenges. This case study demonstrates that with the right approach and tools, businesses can achieve significant enhancements in operational efficiency and productivity.
As industries continue to evolve, the adoption of advanced maintenance systems will be crucial for staying competitive and achieving long-term success.